Hospital Emergency Power Upgrade
- Brian T. Soucy, P.E.
- Nov 18, 2019
- 5 min read
Updated: May 12, 2022
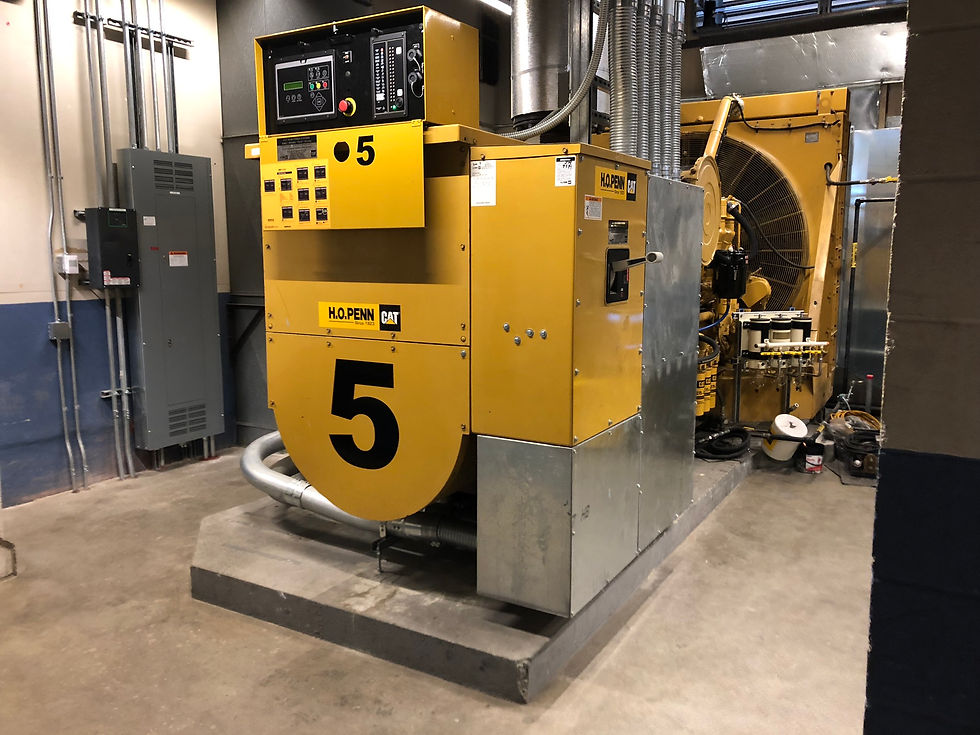
Saint Mary’s Hospital, a Catholic, not-for-profit, community teaching hospital has served patients in Waterbury, CT and the surrounding communities since 1909. Part of Trinity Health Of New England, and member of one of the largest Catholic health care systems in the nation, Saint Mary’s is committed to patient safety and satisfaction, offering the latest in cutting-edge technology, and providing high quality care at the lowest possible cost.
Over its 110-year existence, Saint Mary’s has grown and evolved to better serve its patients, care givers, administration and broader community. Licensed for 347 beds, the Hospital offers a Level II Trauma Center, twenty surgical operating suites, the only pediatric emergency care unit in the region, and critical care units among other services and facilities. The Hospital is also home to the Northwest Connecticut Public Safety Communication Center (NWCTPS) providing 9-1-1 Dispatch Services to 14 towns and cities in the greater Waterbury and Naugatuck Valley area.
Simply put, Saint Mary’s Hospital is a critical resource providing unmatched care and services for the community. So, when it came time to upgrade aging critical infrastructure, Saint Mary’s turned to a team with a proven track record and experience in handling the industry’s most challenging projects. Professionals from Gilbane Building Company and Facilities Engineering Associates pooled their collective expertise in the health care and mission critical industries to construct the solution for Saint Mary’s.
Specifically, the project objective was to replace and consolidate an aging emergency power system, including its diesel generators, paralleling switchgear and the associated power distribution equipment. The new emergency power system had to serve all existing loads, extend emergency power to the Hospital’s air conditioning systems and be upgradeable and redundant. The obvious challenge was implementing the changes while maintaining Hospital operations and limiting risk.
FEA developed an emergency power master plan that included a 3-phased approach. Phase 1 consolidated and replaced the aged equipment and provided the means to support future expansion. Phase 2 extended emergency power to a 900-ton chiller plant. Phase 3 extended emergency power to a 600-ton chiller plant. A schematic design level cost estimate was developed for each phase and Saint Mary’s agreed to fund Phases 1 and 2. Phase 3 was deferred with plans to pair it with other necessary air conditioning upgrades.
The existing emergency power system included a 480V generator plant, consisting of two diesel engine-generators and paralleling switchgear, and an older 208V generator plant, consisting of two smaller diesel engine-generators. The project built a new 480V generator plant to replace both. The new plant included two new generators and refurbishment of an existing generator to provide N+1 redundancy and double the capacity.
The project execution was carefully orchestrated. With no space or budget to build a new generator building, the team had to build a temporary system so the old generators and switchgear could be decommissioned and removed; only then could the new generators be installed. First, the new paralleling switchgear and a temporary generator were installed. The switchgear and controls were installed in the existing generator room and the trailer mounted temporary generator was located in the service courtyard not to block the active loading dock, waste disposal and other operations necessary for a functioning hospital.

The new paralleling switchgear, with its temporary generator, was a critical milestone. The system needed to be fully commissioned to prove to be a reliable source of emergency power before loads were connected. FEA designed the switchgear with a temporary generator mode and it was commissioned according to NFPA 110 acceptance testing requirements. As loads were walked over to the new switchgear, it became the primary emergency power system and was used for the Hospital’s monthly generator and transfer switch tests included in the Hospital’s Joint Commission reporting.
Once the temporary system was commissioned, multiple load swings were required to walk all load off the old system and on to the new. Six load swings were completed during separate 4-hour windows starting at midnight and coordinated with the affected departments. Even though there was no interruption to facility primary and secondary power feeds, each load swing included several hours when loads did not have generator back-up power if utility power were to fail. Go, no-go decisions were made based on patient care requirements, weather, utility company activity, and other Hospital operational considerations. No chances were taken, and contingency plans were made. Even a pumper truck was connected and on standby when the team reworked generator power to the fire pump. In the end, actual exposure times were between 2 to 3 hours, depending on the circuit, and redundant power to the downstream load was maintained throughout.
As load was transferred off the old switchgear and on to the new, the team was able to demolish the old generators and switchgear. Two 1.25MW generators were installed in the place of an old generator and switchgear and a third generator was refurbished. The paralleling switchgear and controls manufacturer, Russelectric, was instrumental in integrating all the generators and configuring the system to provide standby emergency power for the hospital while commissioning the new generator controls.
The final step of Phase 1 included refeeding the 5 loads powered by the old 208V generator plant. To accomplish this the team designed and installed new normal and emergency power substations and transfer switches to replace the obsolete equipment. Next came another five cutovers to walk load off the old plant and on to the new. The challenge here was that each cutover would see a short outage of both normal and emergency power. Even though these circuits mainly powered equipment branch loads, the same meticulous MOP process was executed and temporary power was provided to limit the impact and avoid disruption.
The most difficult cutover was the NWCTPS 9-1-1 Dispatch Service center. The service was powered by a single 400A feed from an obsolete substation and transfer switch. There was no way to perform the cutover safely without de-energizing the main feed. Working with the electrical contractor, McPhee Electric, the team developed an MOP and temporary power feed to safely perform the work on de-energized equipment while keeping the 9-1-1 dispatch operational.
With the 9-1-1- Dispatch refeed complete, the team tackled Phase 2: extending generator power to a 900-ton chiller plant that provides air conditioning to over half the Hospital. Phase 2 included a 2000A transfer switch, load shedding controls and temporary chiller power to perform the installation. Yet another sequence of work carefully coordinated with Hospital operations.
In addition to the new generators, switchgear and circuit cutovers, the project included an upgrade of the emergency power supply system including:
Supervisory, Control and Data Acquisition (SCADA) system for local and remote monitoring and integration with the Hospital’s building automation system for alarm reporting.
Onsite fuel oil storage capacity increase.
Redundant fuel oil pumping system.
Permanent supplemental load banking for Joint Commission compliance.
Automated Joint Commissioning reporting on transfer switches and generator load testing.
A supplemental load bank and temporary load bank connections for generator testing compliance.
New normal and emergency power rooms.
HVAC and pre-action sprinkler systems.
While hospital infrastructure is far from glamorous and can sometimes be overlooked, the Saint Mary’s emergency generator project demonstrates the Hospital’s commitment to quality healthcare and patient safety. Working with the trusted professionals from Gilbane and FEA, who guided them through the process and made it a reality, Saint Mary’s is now better positioned to serve the community for years to come.